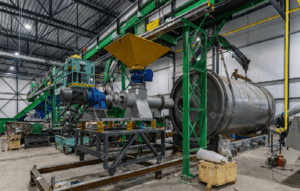
A. Introduction
1. Overview of the Plastic Waste Crisis
Because of its severe ecological, financial, and public health consequences, the plastic trash crisis is a major worldwide environmental problem that has attracted a lot of attention. Millions of tons of plastic garbage are thrown away every year; most of it finds its way in landfills, oceans, and other ecosystems. The results of this plastic contamination are severe:
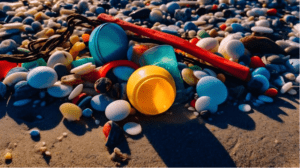
2. Introduction to Plastic Pyrolysis as a Potential Solution
Emerging as a potential fix for the plastic waste dilemma is plastic pyrolysis. Pyrolysis is a thermochemical process wherein polymeric products break down at high temperatures without oxygen. This technique turns trash plastic into useful goods, including char, gas, and fuel oil. The following is a closer view of the possibilities of plastic pyrolysis:
- Reduction of Plastic Waste Volume: Pyrolysis presents a sensible approach to drastically cutting the volume of plastic trash. Turning trash plastic into valuable goods helps to lower environmental pollution and reduce the demand for landfills.
- Resource Recovery: Not only does the pyrolysis process aid in waste management, but it also recovers priceless resources. Pyrolyzed oil is the main good; it can be processed and substituted for traditional fossil fuels. This lessens dependence on non-renewable resources and helps to recuperate energy.
- Environmental Benefits: Comparatively to conventional waste disposal techniques like incineration and landfilling, pyrolysis reduces greenhouse gas emissions. Reducing environmental damage and safeguarding ecological systems depends on stopping plastics from reaching oceans and landfills.
- Economic Opportunities: The commercialization of plastic pyrolysis creates fresh financial possibilities. By means of the sale of pyrolyzed byproducts, industries can invest in pyrolysis technology to develop sustainable business models that not only solve waste management but also provide economic gains.
Understanding the seriousness of the plastic waste situation and investigating the possibilities of plastic pyrolysis would help stakeholders—from legislators and business leaders to environmental advocates—to cooperate to apply sensible ideas for a more sustainable future.
B. The Global Plastic Waste Crisis
Statistics on Plastic Production and Waste Generation
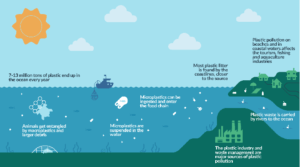
1. Global Plastic Production:
From 2 million metric tons annually in the 1950s to an amazing 367 million metric tons in 2020, plastic manufacturing has exploded.
Should present trends continue, yearly plastic output is expected to exceed 1.1 billion metric tons by 2025.
2. Plastic Waste Generation:
The world produced around 300 million metric tons of plastic garbage in 2020 alone, or the weight of all people taken together.
While 12% of all plastic garbage ever generated has been burned, only roughly 9% has been recycled; the rest, 79%, has gathered in landfills, dumps, or the natural surroundings.
3. Single-Use Plastics:
About half of the plastic generated every year is single-use plastic, which ranges from packaging to straws to plastic bags.
Each year, an estimated 500 billion plastic bags are used globally; less than 1% of these are recycled.
C. Understanding Plastic Pyrolysis
1. Definition and Basic Process of Pyrolysis
Usually free of oxygen, pyrolysis is a thermochemical breakdown process whereby organic molecules are heated in an inert atmosphere. Lack of oxygen stops burning and lets the substance break down into smaller, volatile pieces called pyrolysates.
The process produces three main products: solid char, liquid pyrolysis oil, and non-condensable gases.
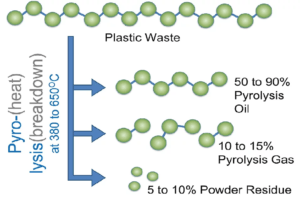
Pyrolysis is a thermochemical conversion method where polymeric materials are superheated at temperatures around 450–800 °C in the absence of oxygen. This process breaks them down into their monomer components and short hydrocarbon chains.
2. Types of Pyrolysis
Fast Pyrolysis
Fast heating rates (usually more than 1000 °C per second) and short residence periods (0.1 to 2 sec) define fast pyrolyzed materials. Designed to enhance liquid fuel output, this technique achieves best yields at about 500 °C.
The rapid processing time reduces the production of solid char and increases the yield of condensible fumes, which can be condensed into pyrolyzed oil. Particularly efficient for biomass, fast pyrolysis can be modified to fit many kinds of plastic waste.
The primary material is a liquid oil; some gas and char are also produced.
Slow Pyrolysis
Slow pyrolysis involves slower heating rates (typically 0.1–1 °C/s) and longer residence times (minutes to hours). The main products are solid charcoal and some liquid and gaseous fuels.
In contrast to fast pyrolysis, slow pyrolysis involves lower heating rates and longer residence times. This method is conducted at lower temperatures (typically between 300°C and 600°C) and is aimed at maximizing solid char production.
Slow pyrolysis is often used for the production of biochar, a carbon-rich material that can be used as a soil amendment or for carbon sequestration. While it yields less liquid fuel compared to fast pyrolysis, it is beneficial for certain applications that prioritize solid products.
Flash Pyrolysis
A form of fast pyrolysis, flash pyrolysis is whereby the feedstock is quickly heated to high temperatures in a few of seconds. This approach aims to minimize the generation of solid residues while nonetheless delivering a high yield of liquid products.
Though it may use different reactor designs and operating parameters to produce even faster thermal breakdown, flash pyrolysis runs under similar ideas to rapid pyrolysis.
Extremely fast heating (>1000 °C/s) and very short residence durations (less than one second) define flash pyrolysis. The main offering is premium pyrolyzed oil with low char output.44, 45,46
3. Process Details of Pyrolysis
The Pyrolysis Process provides a detailed explanation of the pyrolysis process Breakdown of the steps involved (pre-treatment, heating, product recovery) Discussion of the different products obtained (oil, gas, and char). The pyrolysis process for plastic waste can be broken down into the following key steps:
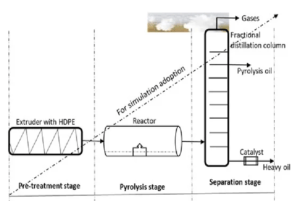
Sorting and separation: The plastic waste is sorted and separated by type, such as PE, PP, and PS, to ensure a more homogeneous feedstock.
Shredding/size reduction: The plastic is shredded or ground into smaller pieces to increase the surface area and improve heat transfer during pyrolysis.
Drying: The plastic may be dried to remove any moisture content, which can affect the pyrolysis process.
Heating and pyrolysis:
The pre-treated plastic is loaded into a pyrolysis reactor, which is heated to the desired temperature (typically 450-800°C) in the absence of oxygen.
As the temperature increases, the long-chain polymer molecules begin to break down into smaller hydrocarbon molecules through thermal cracking.
The specific pyrolysis conditions (heating rate, residence time, temperature) can be adjusted to favor the production of different pyrolysis products.
Product recovery:
The pyrolysis vapors are cooled and condensed to produce a liquid pyrolysis oil. The non-condensable gases, such as methane, ethane, and propane, are collected as a gaseous product.The solid residue, known as char or pyrolysis char, is also collected.
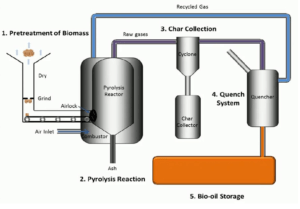
The main products obtained from the pyrolysis of plastic waste are:
- Pyrolysis oil:
- The liquid pyrolysis oil is a complex mixture of hydrocarbons, including aliphatic and aromatic compounds.
- The composition and properties of the pyrolysis oil depend on the type of plastic feedstock and the pyrolysis conditions.
- The pyrolysis oil can be used as a fuel or further refined into various petrochemical products.
- Pyrolysis gas:
- The non-condensable gases produced during pyrolysis, such as methane, ethane, and propane, can be used as a fuel source or further processed.
- Pyrolysis char:
- The solid residue, or char, is a carbon-rich material that can be used as a fuel, a reducing agent in metallurgical processes, or as an adsorbent material.
The relative proportions of these products can be adjusted by optimizing the pyrolysis conditions, such as temperature, heating rate, and residence time, to meet specific requirements or desired product yields.
D. Plastic Waste Suitable for Pyrolysis
A flexible method able to manage a range of plastic waste kinds is plastic pyrolysis. Still, the kind of plastic feedstock utilized greatly affects the end products’ quality and efficiency. These are the primary forms of plastic garbage fit for pyrolysis:
Polyethylene (PE):
High-Density Polyethylene (HDPE): Commonly found in products like milk jugs, detergent bottles, and plastic pipes. HDPE is highly suitable for pyrolysis due to its high hydrocarbon content.
Low-Density Polyethylene (LDPE): Found in products like plastic bags, plastic films, and squeeze bottles. LDPE is also a good candidate for pyrolysis, producing a substantial amount of liquid fuel.
Polypropylene (PP):
This type of plastic is used in products such as yogurt containers, bottle caps, and automotive parts. PP has a high calorific value, making it an excellent feedstock for pyrolysis.
Polystyrene (PS):
Found in products like disposable coffee cups, plastic food boxes, and insulation materials. PS is suitable for pyrolysis due to its ability to decompose into valuable liquid hydrocarbons.
Polyvinyl Chloride (PVC):
Commonly used in pipes, cable insulation, and medical equipment. However, PVC is less preferred for pyrolysis because it releases hydrochloric acid (HCl) during the process, which can be corrosive and harmful. Special handling and pre-treatment are required to neutralize or remove chlorine content.
Polyethylene Terephthalate (PET):
Mainly used in beverage bottles, food containers, and synthetic fibers. PET is suitable for pyrolysis, but it might require more precise temperature control to stabilize the process.
Mixed Plastic Waste:
This includes municipal solid waste, which consists of various types of plastic mixed together. While mixed plastics can be processed through pyrolysis, the quality of the end products may vary. Pre-sorting or blending might be necessary to optimize the pyrolysis process.
Multi-layer and composite plastics:
These are commonly used in packaging materials that combine different types of plastics and sometimes incorporate layers of aluminum or paper. Pyrolysis can process these materials, but the complexity of the feedstock can affect the efficiency and quality of the output.
Considerations for Optimal Pyrolysis:
- Purity: Higher purity plastics typically yield better results, as contaminants can affect the decomposition process and the quality of the end products.
- Moisture Content: Plastics should be dry before pyrolysis to prevent unwanted reactions and improve the efficiency of the thermal breakdown process.
- Additives: Some plastics contain additives such as colorants, stabilizers, and fillers, which can affect the pyrolysis process. These may require pre-treatment or special handling.
Understanding and optimizing the several kinds of plastic feedstocks helps the pyrolysis process be customized to maximize outputs and increase the general feasibility of turning plastic waste into useful resources.
E. Plastic Waste Unsuitable for Pyrolysis
Yes, there are some limitations in the types of waste that can be effectively treated using pyrolysis:
Heterogeneous Waste: Pyrolysis works best with homogeneous feedstocks, as the process is sensitive to the composition and properties of the input material. Highly heterogeneous waste, such as mixed municipal solid waste, can be challenging to process efficiently.
Wet Waste: Pyrolysis is generally not well-suited for treating wet or high-moisture content waste, as the presence of water can disrupt the thermal decomposition process and reduce the overall efficiency.
Hazardous Waste: Certain types of hazardous waste, such as those containing heavy metals or persistent organic pollutants, may not be suitable for pyrolysis due to the potential for the release of toxic substances during the thermal treatment.
Chlorinated Waste: Waste streams containing high levels of chlorine, such as polyvinyl chloride (PVC), can be problematic for pyrolysis, as the chlorine can lead to the formation of corrosive and environmentally harmful compounds, like dioxins and furans.
Inorganic Waste: Pyrolysis is primarily designed to treat organic waste materials, and it may not be as effective in processing inorganic waste, such as metals or ceramics, which do not undergo thermal decomposition in the same way.
Large or Bulky Waste: Pyrolysis reactors have size limitations, and processing large or bulky waste items may require pre-treatment, such as shredding or size reduction, to ensure efficient thermal conversion.
These limitations can vary depending on the specific pyrolysis technology and the design of the processing facility. Careful characterization and pre-treatment of the feedstock may be necessary to ensure the successful and efficient application of pyrolysis for waste management.
F. Environmental Benefits of Plastic Pyrolysis
Reduction of plastic waste:
Pyrolysis can divert large quantities of plastic waste from landfills and oceans, helping to address the global plastic pollution crisis.
By converting plastic waste into valuable products, pyrolysis reduces the need for virgin plastic production, which in turn reduces the amount of plastic waste generated.
Conversion of waste into energy resources:
The pyrolysis process converts plastic waste into liquid fuels, gases, and solid char, all of which can be used as energy sources.
This allows for the recovery of the inherent energy content of the plastic waste, which would otherwise be lost through landfilling or incineration.
Lower greenhouse gas emissions:
Compared to incineration, which releases significant amounts of carbon dioxide, pyrolysis has a lower carbon footprint.
The pyrolysis process does not involve the direct combustion of the plastic waste, resulting in lower greenhouse gas emissions.
The liquid fuels and gases produced through pyrolysis can also displace the use of fossil fuels, further reducing the overall carbon impact.
Production of clean-burning fuels:
The liquid fuels and gases generated from plastic pyrolysis can be used as clean-burning alternatives to traditional fossil fuels.
These pyrolysis-derived fuels can have lower emissions of pollutants like sulfur, nitrogen oxides, and particulate matter compared to conventional fossil fuels.
The use of these clean-burning fuels can contribute to improved air quality and reduced environmental impact.
Government policies and incentives play a crucial role in promoting the adoption of plastic pyrolysis and other advanced recycling technologies. Measures such as landfill taxes, extended producer responsibility schemes, and subsidies for the use of recycled plastics can help create a favorable environment for the growth of the plastic pyrolysis industry.
G. Disadvantages of pyrolysis
Here are some of the main disadvantages of pyrolysis:
High Energy Consumption: Pyrolysis requires high temperatures, typically between 400-900°C, which requires a significant amount of energy input. This can make the process energy-intensive and costly.
Complexity of the Process: Pyrolysis involves complex chemical and physical reactions, making it challenging to optimize and control the process to achieve the desired product yields and quality.
Potential Environmental Concerns: Pyrolysis can produce emissions, such as particulates, volatile organic compounds (VOCs), and greenhouse gases, which may require additional treatment or mitigation measures to comply with environmental regulations.
Limited Feedstock Flexibility: Pyrolysis is often optimized for specific feedstocks, and the process may not be as effective or efficient when dealing with a diverse range of feedstocks or varying compositions.
Residue Management: Pyrolysis can produce solid residues, such as char or ash, which may require further processing or disposal, adding to the overall cost and environmental impact of the process.
Capital-Intensive: Pyrolysis plants can be expensive to build and operate, with significant upfront investment required for the specialized equipment and infrastructure.
Scalability Challenges: Scaling up pyrolysis plants can be challenging, as the process may not always maintain the same efficiency and product yields at larger scales.
Regulatory Hurdles: Pyrolysis may face regulatory challenges, particularly in terms of emissions control, waste management, and product certification, which can add complexity and cost to the implementation of the technology.
Overall, while pyrolysis offers potential benefits, these disadvantages need to be carefully considered and addressed to make the process more economically and environmentally viable.
H. Case Studies
Case Studies and Real-World Applications Showcase successful plastic pyrolysis projects highlight the impact of these projects on the environment Discuss the role of government policies and incentives.
Plastic Energy (Spain):
Plastic Energy operates two commercial-scale pyrolysis plants in Spain that convert mixed plastic waste into a hydrocarbon oil called TACOIL.
The TACOIL is then used as a feedstock for new plastic production, enabling a circular economy for plastics.
The company’s process can handle a wide range of plastic waste, including films, bags, and multilayer packaging.
Plastic Energy’s plants have the capacity to process 20,000 tons of plastic waste per year, diverting it from landfills and incineration.
The Spanish government provides tax incentives and subsidies for the use of recycled plastics, supporting the growth of Plastic Energy’s operations.
Recycling Technologies (UK):
Recycling Technologies has developed a modular pyrolysis technology that can process a wide range of plastic waste, including films, pots, tubs, and trays.
The company’s RT7000 unit can process up to 7,000 tons of plastic waste per year, producing a hydrocarbon oil that can be used as a feedstock for new plastic production.
Recycling Technologies has partnered with several local authorities in the UK to establish plastic waste collection and processing hubs, improving the availability of feedstock for their pyrolysis plants.
The UK government’s plastic packaging tax, which charges a fee for using virgin plastic, has provided an incentive for companies to adopt recycling technologies like pyrolysis.
Brightmark (United States):
Brightmark operates a commercial-scale pyrolysis plant in Indiana, USA, that can process up to 100,000 tons of plastic waste per year.
The plant produces a range of products, including a liquid fuel, a wax, and a solid char, which can be used in various applications.
Brightmark has partnered with several municipalities and waste management companies to secure a reliable supply of plastic waste feedstock for its operations.
The US federal government offers tax credits and incentives for the production of renewable fuels, which has helped support the growth of Brightmark’s pyrolysis business.
These case studies demonstrate the potential of plastic pyrolysis to divert plastic waste from landfills and incineration, while also providing a sustainable source of raw materials for the petrochemical industry.
I. Traditional plastic waste collection vs Pyrolysis
1. Overview of Mechanical Recycling Processes
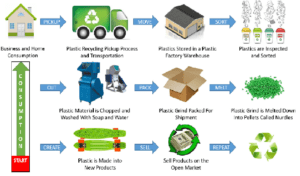
Among the most commonly used techniques for processing plastic trash is mechanical recycling. This approach consists of multiple important phases:Mechanical recycling is one of the most common methods employed to process plastic waste. This method involves several key stages:
Collection and Sorting: Plastic garbage is gathered from homes, companies, and industrial operations, among other places. It is next arranged according to type of polymer, color, and cleanliness. Manual sorting as well as automated systems utilizing technologies such as density separation and infrared spectroscopy can be accomplished.
Shredding and Washing: Sorted plastics are shredded into tiny flakes to aid in washing. To eliminate food residue, labels, and other non-plastic objects, washing is really vital.
ls.
Melting and Pelletizing: Melting and pelletizing the clean plastic flakes follows next, which are extruded into pellets. Raw materials for newly produced plastic goods come from these pellets.
2. Challenges Faced by Mechanical Recycling
Despite its widespread use, mechanical recycling faces several significant challenges:
Contamination and Degradation:
Contaminants: Mechanical recycling calls for highly clean plastic streams. Food particles, metals, and other non-compatible polymers, among other contaminants, can seriously affect the quality of the recycled goods. For example, a tiny level of PVC pollution in a PET recycling stream could ruin the whole batch.
Polymer Degradation: The recycling process heats the polymer chains, which can lead to their thermal breakdown. The mechanical qualities of the recycled plastic thus suffer, including tensile strength and flexibility.
Collection and Sorting Inefficiencies:
Human Error: Manual sorting is labor-intensive and prone to human error, therefore producing mixed and contaminated recycling streams.
Technological Limitations: Though automatic sorting systems exist, their efficacy is not always perfect. For instance, black plastics’ color—which absorbs near-infrared radiation—makes them challenging to sort using infrared technology.
Economic Viability:
High Costs:
Recycling’s steps of collecting, sorting, and processing come with large expenses. Furthermore, recycling is less economically appealing since virgin plastic’s cost often rivals, if not less than, that of recycled plastic.
3. Inefficiency with Mixed Plastics
One of the most pressing issues in mechanical recycling is the inefficiency related to mixed plastics:
Diverse Polymer Types: Consumer goods are produced from a broad spectrum of polymers, including PET, HDPE, LDPE, PP, and PVC, among others. These several kinds mix to greatly complicate the recycling process since their melting points and chemical characteristics differ.
Layered and Composite Plastics: Many goods use multilayer or composite plastic materials, which mix many kinds of polymers or blend plastic with other materials like metal. Mechanical recycling of these is particularly difficult since the components cannot be readily separated.
4. Downcycling and its Consequences
Mechanical recycling sometimes leads to downcycling, unlike closed-loop recycling, whereby materials are recycled into products of the same type and quality.
Quality Degradation: Recycled plastics typically show poorer material qualities than virgin plastics. For instance, instead of new PET bottles, recycled PET might be converted into lower-grade goods such as clothes fibers. Because they cannot satisfy the strict performance criteria of the original products, recycled materials are thus often downcycled.
Limited Applications: Downcycling reduces the uses for which the recycled material can be put. With every cycle of recycling, the quality of the recovered plastic decreases; reducing its useful lifetime for high-performance uses. This eventually results in the material’s unavoidable disposal—often in landfills or incinerators.
Environmental Impact: Downcycled plastics fail to completely offset the environmental load caused by plastic trash since its limited applications and lower usable life mean Additionally, downcycled goods help sustain the cycle of plastic manufacture and waste generation by contributing to ongoing demand for virgin plastics.
In essence, mechanical recycling has significant restrictions, even if it is quite important for controlling plastic waste. Challenges such as contamination, polymer degradation, inefficiencies with mixed plastics, and downcycling underline the need for alternate and complementary recycling technologies, including chemical recycling and plastic pyrolyzes, to more properly handle the plastic waste situation.
Hi there, I just came across your new site and saw that you’re getting started with WordPress – something I’m well experienced in! It’s always thrilling to see how new websites unfold. Building a website is not always a simple task – are you doing this on your own or do you have a developer to help you out? Regardless, I can’t wait to see how your site progresses. If you ever need to discuss anything WordPress-related, feel free to drop me an email at contact@ghazni.me, or message me on WhatsApp or Telegram.
Kind regards,
Mahmud Ghazni
WhatsApp: +880 1322-311024
Telegram: https://t.me/ghaznidev
Amazing blog! Do you have any suggestions for aspiring writers?
I’m planning to start my own site soon but I’m a little lost on everything.
Would you recommend starting with a free platform like WordPress or go for
a paid option? There are so many choices out there that I’m completely confused ..
Any recommendations? Bless you!
[…] impact of waste generation, conserves resources, reduces pollution, and addresses climate change. Embracing recycling practices, composting, and reducing single-use plastics are effective strategies to minimize waste and […]
Awesome page with genuinely good material for readers wanting to gain some useful insights on that topic! But if you want to learn more, check out Webemail24 about PR Marketing. Keep up the great work!
[…] For instance, chemical recycling processes, such as depolymerization and pyrolysis, can break down plastic waste into its basic building blocks, allowing them to be used as feedstock for the production of new […]
Having read your posts. I believed you have given your readers valuable information. Feel free to visit my website Seoranko and I hope you get additional insights about Social Media Marketing as I did upon stumbling across your site.
arjuna4d arjuna4d arjuna4d
Very nice post. I just stumbled upon your blog and wished to say that I have truly enjoyed browsing your blog posts.
In any case I will be subscribing to your feed and I hope you
write again very soon!
kinghorsetoto kinghorsetoto kinghorsetoto
This is the perfect web site for everyone who hopes to understand this topic.
You understand so much its almost tough to argue with you (not that I personally would want to…HaHa).
You certainly put a new spin on a topic that has been written about for years.
Excellent stuff, just great!
gacor77 gacor77 gacor77
Genuinely no matter if someone doesn’t be aware of after that its up to other users that they will assist, so here it takes place.
jikoshoukai jkt48 jikoshoukai jkt48
jikoshoukai jkt48
Hi there to all, the contents existing at this site are actually awesome for people experience,
well, keep up the good work fellows.
Keep on writing, great job!
This piece of writing is really a pleasant one it assists new internet viewers, who are wishing for blogging.
Hi everyone, it’s my first pay a quick visit at this site, and paragraph is genuinely fruitful designed for me, keep up posting
these articles or reviews.
Thanks for sharing your thoughts about 1. Regards
Just desire to say your article is as astonishing. The clarity for your put
up is simply spectacular and that i can assume you’re a professional
on this subject. Fine along with your permission let me to clutch your feed
to stay up to date with forthcoming post. Thank you a million and please keep up the
rewarding work.
Wonderful blog! I found it while browsing on Yahoo
News. Do you have any suggestions on how to get listed
in Yahoo News? I’ve been trying for a while
but I never seem to get there! Many thanks
Marvelous, what a web site it is! This web site presents helpful information to
us, keep it up.